SQC service makes Sample making as simple as 1, 2, 3.
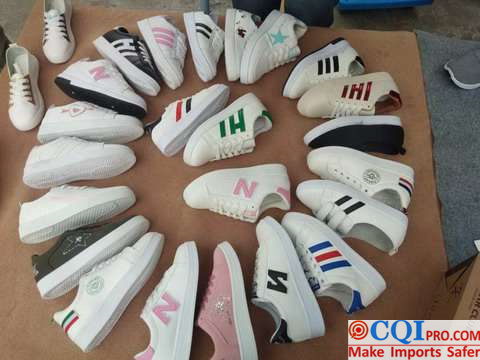
Importers will magically discover the following facts.:
- Sample development duration, halved;
- Sample making follow-up workload is reduced by 90%;
- Cross-border courier fees are reduced by 90%;
- No jet lag, no language barrier;
- There is an additional quality management office in China serve for you
- Cross-border supply chain management has been directly upgraded to several levels.
Refer to below for details, then know why SQC service can really help you,:
Step 1, Importers ( CQI’s clients) contact the factory to reach a preliminary purchase intention.
Importers: Importers contact the customer’s factory to reach a preliminary purchase intention, both sides then enter the sample development stage.
SQC Technicians: /(CQI does not intervene)/
Factories: Factories communicate with importers to determine cooperation intention.
Step 2, SQC (Sample Quality Check) of CQI began to intervene in sample development.
Importers: Importers send the requirements of sample development to SQC technicians and inform the factory. The SQC technicians of CQI will be responsible for the follow-up of sample development.
SQC Technicians:
- SQC technicians, who get the importers’ requirements,
- and sort them into technical documents with quality know-how.
- SQC technicians contact the factory, inform them of the service process and the points for attention in for cooperation.
Factories: Factories receive technical documents and make preliminary preparations.
Step 2-1 Early stage of SQC service (early stage of sample production)
Importers: If Importers have updated requirements of sample development, send them to SQC technicians in time.
SQC Technicians:
- SQC technicians, sort out the updated requirements of sample development.
- SQC technicians, keep closely contact with the factory in time through email, telephone and App
- to supervise the factory’s sample production progress.
- SQC technicians inform importers of the updated progress of sample making.
Factories: Factories keep communication with SQC technicians, who will check whether the sample making is conform with the importer’s requirement.
Customer benefits:
- SQC’s technicians take full advantage of time-difference-free, mother tongue, professional quality background , and
- efficiently follow up the sample making, which can save the purchasing staff a lot of working time for importers, and
- more focus on the more meaningful work.
- SQC technicians have strong technical background in quality, which is conducive to promoting the progress of sample making.
Step 2-2 Mid-term of SQC service (sample preliminary production is completed and mailed to CQI office)
Importers: /
SQC Technicians:
- SQC technicians, according to product quality and inspection industry requirements,
- carry out sample quality checking (SQC) on samples to check whether the samples meet the importers’ requirements for sample making (Compliance 1), and
- whether the samples meet industry quality requirements (Compliance 2).
- A professional and detailed SQC report and related videos will be sent to importers by SQC technicians by email.
- Importers can get an in-depth understanding of whether the quality of the sample meets the requirements and
- decide whether the sample needs to be further modified according to the SQC report and vidoes,
- but without cross-border mailing the sample from the factory in china.
Factories: /
Customer benefits:
- SQC reports and videos are professional and detailed,
- so that for importers, sample confirmation is no longer limited to the surface, which also
- help importers to have a deeper understanding of the internal quality of samples, beside the external quality sense.
- With CQI’s SQC service, importers just by read and study the SQC report and videos can decide whether samples.
- As a result, importers don’t need to pay cross-border courier fees that is almost worthless.
- More importantly, the sample confirmation time is greatly reduced.
- Moreover, SQC’s reports and videos are convenient for importers to communicate with end customers or interested parties
- in a professional way to discuss whether the final samples meet the requirements.
Step 2-3 Later stage of SQC service (modification of samples)
Importers: Importers read SQC report and video to determine whether the sample needs further modification.
SQC Technicians:
- SQC technicians, add importer’s requirement for sample modification and update requirements,
- communicate with the factory efficiently through email phone and SNS,
- supervise them to implement the importers’ sample modification opinions.
- SQC technicians inform the importers of the sample modification progress in the factory by email.
Factories: Factories keep communication with SQC technicians, feedback the details and the progress of sample modification.
Step 3, Final confirmation of samples
Importers: Importers inform SQC team which samples need to be cross-border mailed to the importers office.
SQC Technicians:
- SQC technicians, arrange to package and cross-border mail the samples specified by importers,
- and provide express delivery number to facilitate customers to know logistics information.
Factories: /